هم اکنون!
زمان آزمون
فرا رسیده است.
برای نخستین بار دستگاه آزمون سختی دینامیک خانواده قطعات ضربهگیر با محدوده فرکانسی 100 هرتز در کشور توسط شرکت متینکیمیا طراحی و مورد بهرهبرداری قرار گرفت.
تجهیزات آزمون دینامیک قطعات لاستیکی بنا به ماهیت عملکردی، فرکانس بالا و دامنه ارتعاشات گسترده از طراحی و ساخت پیچیدهای برخوردارند.
بارگذاری یک ارتعاش سینوسی و یکنواخت بدون نوسانات جانبی، حذف ارتعاشات غیر محوری، اثرات فیکسچر و اتصالات قطعه، نوسانات و نویز حاصل از تامین منبع حرکتی (درایوینگ)، تامین توان مناسب در گستره کامل فرکانسی و دامنه ارتعاش، حذف نویز الکتریکی و پدیده EMC، نرخ نمونه برداری و تفکیک مقادیر داده از اغتشاشات مکانیکی و الکتریکی و... برخی از دشواری های موجود در طراحی و ساخت دستگاه آزمون سختی دینامیک لاستیک و فلز است. کلیه موارد طراحی در کنار هزینه بالای سخت افزاری و نرم افزاری دستگاه فرآیند تامین این دستگاه را در صنایع خودروسازی با مشکلات عدیدهای مواجه کرده است. از سوی دیگر الزام مشتری جهت انجام آزمون سختی دینامیکی قطعات لاستیکی و ضربه گیرها، استقرار دستگاه مربوطه را برای قطعهسازان به یک ضرورت تبدیل کرده است. تا پیش از این به دلیل سطح فناوری بالا کلیه تولید کنندگان اقدام به خرید دستگاه از منابع خارجی نموده بودند که در برخی از مواقع نیز به دلایل مختلف از جمله وجود تحریمها مانع از ارائه خدمات آزمایشگاهی مطلوب میگردید. شرکت متین کیمیا با فراهم آوردن زیرساخت های لازم توانست برای نخستین بار طراحی و ساخت دستگاه مذکور را در داخل کشور به انجام رساند.
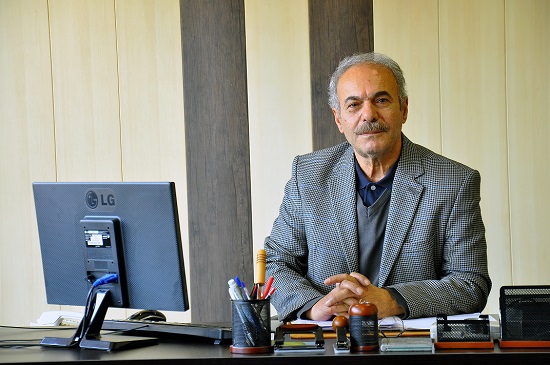
«حسن فرحبخش» مدیر عامل کارخانه متینکیمیا تحصیلات دانشگاهی خود را در دو رشته مکانیک و مدیریت گذرانده و از سال 1364 وارد عرصه تولید شده است.
وی شروع فعالیت قطعهسازی در شرکت متینکیمیا را اینگونه توصیف میکند:
در سال 1373 قطعهسازی را با ثبت شرکت متینکیمیا آغاز کردیم. اگرچه شرکت را در تهران ثبت کردیم اما به دلایلی کارخانه در اصفهان راهاندازی شد. متینکیمیا کار خود را با تولید قطعات زیر مجموعه سیستم سوخت رسانی با شرکت سازهگستر سایپا آغازکرد.
در آن سالها و در ابتدای کار تجهیزات سختافزاری به صورت امروزی نبود. پرسهای وکیوم و تزریقی به شکل فعلی وجود نداشت. تجهیزات ما پرسهای هیدرولیک معمولی بودند که اکثراً اپراتورمحور بودند. عملکرد کارشناس و اپراتور دستگاه در روند تولید قطعات بسیار تأثیرگذار بود. بنابراین نیاز به وجود کارشناسان و متخصصان زبده از همان ابتدا احساس میشد.
وی ادامه میدهد: هنگامی که تولید قطعات پلیمری و اکسترودری را آغاز کردیم، فقط دانش و تکنولوژی ساخت قطعات تکلایه در ایران بود. متینکیمیا اولین شرکت داخلی بود که توانست از طریق تعامل و همکاری با شرکتهای خارجی دانش تولید قطعات اکسترودری چندلایه را به ایران وارد کند. علاوه بر این در سال 1378 با کسب تأییدیه از کارشناسان شرکت کیای کره برای اولینبار توانستیم مجموعه حبابگیر از مجموعه سوخترسانی و کلاهک کمک فنر پراید را در داخل تولید کنیم.
تحریم، فرصتی برای ارتقای تولیدات متینکیمیا
فرحبخش معتقد است تحریم در کنار ناملایمتهایش به شرکت آنها فرصت تولید قطعاتی را داد که تا پیش از این در داخل تولید نمیشد.
بحث ارتقای کیفیت از سال 1381 با جدیتی بیش از پیش دنبال شد. مهندس فرحبخش یکی از عوامل اصلی این امر را حمایت گروه سایپا از شرکتهای زنجیره تأمین به منظور افزایش کیفیت دانست و گفت: در حوالی سالهای 80 و 81 شرکت سایپا در جهت ارتقای دانش فنی شرکتهای تأمینکننده گام مثبتی برداشت و با حمایتهای مالی شرکتها را به ارتقای مدیریت کیفیت، دانش فنی و زیرساختهای مهندسی ترغیب میکرد. متینکیمیا اولین شرکت از زنجیره تأمینکنندگان قطعات خودرو در اصفهان بود که در سال 1382 استاندارد ISO/TS 16949 را دریافت کرد.
بعد از ارتقای مدیریت کیفیت متوجه شدیم تولید با ابزار و ماشینآلات موجود توجیه اقتصادی ندارد. پس برای بهینهسازی استانداردها و ارتقای کیفیت، بهینهکردن تجهیزات و ماشینآلات کارخانه سرمایهگذاری بزرگی صورت گرفت.
اینگونه بود که تولید و کیفیت در کارخانه متینکیمیا وارد عرصه جدیدی شد.
از مهمترین تجهیزاتی که در آن سال به خط تولید کارخانه متینکیمیا اضافه شد دستگاه تزریق و وکیوم لاستیک بود. دستگاه وکیوم لاستیک قادر است در خلأ 600 میلیمتر جیوه تمامی حبابهای موجود در قالب را برطرف کند. کیفیت محصول نهایی که با استفاده از دستگاه وکیوم لاستیک تولید میشود قابل مقایسه با انواع دیگر نیست. در حال حاضر در ایران به ندرت این دستگاه یافت میشود. وقتی تجهیزات و ماشینآلات مدرن شد، در پی آن کلیه قالبها نیز تغییر کرد و در حقیقت در سال81 انقلابی در شرکت رخ داد که به افزایش کمّی و کیفی تولید منجر شد.
تجهیزات و قالبهای جدیدی که از کشور تایوان خریده شده بود شرایط تولید را بهبود بخشید. بهبود شرایط تولید باعث شد با گذشت سالها محصولات متینکیمیا علاوه بر ثبات در حفظ کیفیت کاهش قیمت نیز داشته باشند. گذشت زمان موجب کاهش قیمت برخی محصولات این کارخانه شد.
مهندس فرحبخش در این مورد افزود: تجهیزات جدیدتر امتیازاتی مانند کاهش زمان پخت، افزایش کتیبهها و ... را به خط تولید میدهند که میتوان با آنها ثبات قیمت یا حتی کاهش آن را توجیه کرد. بخشی از کیفیت با ارتقای تجهیزات و ماشینآلات تحقق گردید اما برای تحقق کامل آن احساس کردیم به تجهیزات آزمون و دستگاههای کنترلی نیاز داریم. آزمایشگاهمان را بهگونهای تجهیز کردیم که بتوانیم آزمونهای مورد نیاز محصولات خودمان را اعم از آزمونهای دینامیکی، استاتیکی، دوام و شرایط محیطی و ایجینپ را انجام دهیم. متناسب با نیازهای مجموعه تجهیز آزمایشگاه و واحد کنترل کیفیت صورت گرفت. تجهیزاتی از قبیل رئومتر، دستگاه آزمون رئومتر، دستگاه کشش/ فشار، سختیسنج، انواع محفظههای شرایط محیطی و حرارتی و برودتی که تا دمای 40- درجه سانتیگراد را پوشش میدهند، فراهم شد. البته در زمینه استفاده از تجهیزات آزمون رابطه بسیار خوبی با مراکز علمی برقرار کردیم. با دانشگاه صنعتی اصفهان به ویژه استادان و دانشجویان دانشکده شیمی و پلیمر ارتباط تنگانگی داریم.
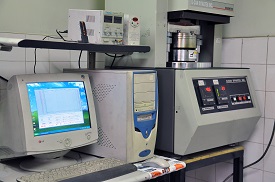 |
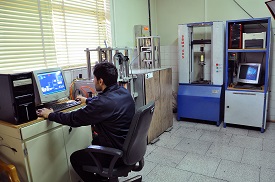 |
وقتی سرمایهگذاریها در بخش تولید و کنترل کیفیت انجام شد، شرایط خوبی مهیا گردید تا قطعات جدیدی را برای تولید به دست بگیریم. اما متأسفانه بحران اقتصادی سالهای 90-89 موجب تغییراتی در برنامهریزیهای شرکت شد. این تغییرات که در شرایط تورم و رکود اقتصادی اتفاق افتاد باعث شد استراتژی حفظ وضعیت موجود را در پیش بگیریم که خوشبختانه در این مدت نه تنها توانستیم مجموعه را حفظ کنیم، بلکه توانستیم بحران تحریم را به یک فرصت تبدیل کرده و با مهندسی معکوس، برخی قطعات را که پیش از آن به صورت CKD وارد کشور میشد، در داخل تولید کنیم. مانند: ضربهگیر پلی یوروتان تیبا، کلاهک تیبا، یاتاقان و قطعات مدول برلیانس H300 و H200 و... که برخی از آنها در داخل کشور تولید نمی شد. تحریمها این فرصت را برای ما ایجاد کرد که قطعات را در واحد فنی مهندسی معکوس کنیم، نمونههای اولیه آزموده شد و به تولید انبوه رسید.
وی درباره محصولات فعلی این شرکت میگوید: عمدهترین محصولات ما قطعات ترکیبی لاستیک و فلز است. در این باره تجربۀ بیشتری کسب کرده و دانش بیشتری داریم. مذاکراتی هم با یک شرکت کرهای داشتهایم تا در این زمینه با آنها همکاری کنیم و از دانش و تخصص آنها در مورد قطعات لاستیکی- فلزی بهره ببریم. همکاری ما با این شرکت برای بومیسازی دانش فنی و تکنولوژی آنهاست. شرکت مذکور از معتبرترین شرکتهای فعال در ساخت قطعات خودرو است. یک تولیدکننده OE محسوب میشود و برای برندهای مطرحی همچون هوندا و کیا محصول تولید میکند.
مدیرعامل شرکت متینکیمیا ادامه میدهد: در حال حاضر ساخت قطعات تعلیق انواع خودروهای سایپا را به عهده داریم. با شرکت ایرانخودرودیزل هم قراردادهای بسیاری منعقد کردهایم.
مهندس فرحبخش درباره دیگر تولیدات این شرکت میافزاید: دسته موتورهای ترکیبی از آلومینیم، لاستیک و فلز، دسته موتورهای گیربکس، دسته موتورهای اتاق و دسته موتورهای موتور جلو و عقب از دیگر تولیدات شرکت متینکیمیا است. بیشتر تخصص ما در تولید قطعات لاستیکی و فلزی به صورت ترکیبی است اما تولید قطعات لاستیکی به صورت تخصصی و پیشرفته در برنامه آتی شرکت قرار دارد.
این صنعتگر در خصوص زیرساختهای شرکت افزود: در حال حاضر مساحت کارخانه حدود 3هزار و 960 متر مربع است که 2هزار و500متر آن زیربنا است. قسمت اداری حدود 300متر است. 250متر در طرح توسعه اضافه خواهد شد. بخشهای دیگر نیز سالن تولید و انبار است.
وی چارت سازمانی و زیرساختهای این شرکت را توضیح میدهد و میافزاید: نزدیک به 90 نفر پرسنل داریم که حدود 30 درصد آنها ستادی هستند. چارت سازمانی هم به این صورت است که شرکت در کنار هیأت مدیره و مدیر عامل، مشاور مالیاتی دارد و همۀ امور تولید بازرگانی، آزمایشگاه، تضمین کیفیت، کنترل کیفی و حتی بازرگانی به جز بخش مالی به مدیر کارخانه تفویض اختیار شده است.
در حال حاضر عمده محصولات شرکت متینکیمیا تولید انواع سیستمهای تعلیق است. مهندس فرحبخش در این خصوص میگوید: در حال حاضر با توجه به سفارشات و قراردادی که داریم ظرفیت کاریمان تقریباً پر است، اما طبق استراتژی و برنامه، خریداری یک خط پلییوروتان را در دست کار داریم که بتوانیم قطعات پلییوروتان را با هدف تولید قطعات ضربهگیر تولید کنیم. زیرا قطعات پلییوروتانی که در حال حاضر در ایران تولید میشوند نمیتوانند آزمون دوام را به خوبی پشت سر بگذارند.
مدیر عامل شرکت متینکیمیا در خصوص استراتژی تولید این شرکت یادآور میشود: افزایش ماشینآلات و عقد قراردادهایی را در دستور کار داریم و منتظر برقراری ارتباط با شرکتی کرهای هستیم.
هدف ما انتقال دانش فنی شرکتهای خارجی و صاحب فناوری به داخل کشور است. |
وی در مورد سهم صنعت لاستیک از دانش خارجی میگوید: به نظر من در حال حاضر این موضوع به دو بخش تأمین مواد اولیه و ماشینآلات تقسیم میشود؛ درباره مواد اولیه، باید بگویم قسمت اعظم مواد اولیه لاستیک در حقیقت لاستیک طبیعی (natural rubber) بنا به شرایط اقلیمی در ایران تولید نمیشود و آنچه از مواد اولیه در ایران تولید میشود به تنهایی کافی نیست. اما از نظر ماشینآلات و تجهیزات، چند سالی است تجهیزات مهمی مثل ماشین تزریق لاستیک در کشور تولید میشود. هدف ما انتقال دانش فنی آنها به داخل کشور است.
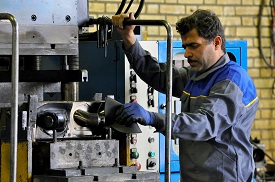
شرکت متینکیمیا از باسابقهترین شرکتهای فعال در تولید قطعات لاستیک و فلز است و در حال حاضر قرارداد تولید ۱۰ تا ۱۲ قطعه با شرکت سازهگستر و بیش از 40 قرارداد با شرکت ایرانخودرو دیزل دارد. بررسی میزان رضایت از محصول نشان میدهد محصولات این شرکت با درصد رضایت بالایی از جانب مشتریان در زمره گروه سبز یعنی محصولات خودبازرس قرار دارند.
مدیر عامل میتنکیمیا در اینباره ادامه میدهد: قطعات تولیدی ما بخشی از یک مجموعه هستند. اگر مشتری نارضایتی از مجموعه قطعات داشته باشد قطعه شرکت ما را هم ممکن است شامل شود. پس از اینکه از خدمات پس از فروش برمیگردد و آمارش را مطلع میشویم، سیستمی وجود دارد که طی آن، نماینده مشتری با نماینده کیفی و خدمات پس از فروش و نماینده شرکت به بررسی میپردازند که طبق بررسیها، درصد نارضایتیها از محصولات متینکیمیا هرگز از 10 و 15 درصد افزایش پیدا نکرده است.
بررسی میزان رضایت از محصول نشان میدهد محصولات این شرکت با درصد رضایت بالایی از جانب مشتریان در زمره گروه سبز یعنی محصولات خود بازرس قرار دارند. |
مدیرعامل شرکت متینکیمیا دربارۀ رمز این موفقیت میگوید: معتقدم هرجا مدیریت ارشد به سیستمهای مدیریت کیفیت اعتقاد داشته باشد و هرجا بتواند سیستم ISO/TS 16949 و سیستم مدیریت کیفیت را به صورت کامل اجرا کند، آن مجموعه قطع به یقین موفق است.
مشتری در رأس امور ما قرار دارد و اگر مشتری نباشد ما هم نیستیم. پس رضایت مشتری اولویت اول ماست و اگر مشکل کیفی وجود داشته باشد در اولین فرصت نماینده شرکت حضور پیدا کرده و اقدامات اصلاحی انجام میشود. |
به گفته وی، نقش فناوریها و دانش فنی خارجی در ارتقای کیفیت را نمیتوان نادیده گرفت. وقتی قطعهای را مهندسی معکوس میکنیم از دانش فنی آن استفاده و دانش فنی آن را بررسی میکنیم؛ وقتی قطعهای را میآوریم ابتدا آن را آنالیز میکنیم، مواد را تشخیص میدهیم، آزمونهای مقایسهای انجام میدهیم و همچنین از طریق بستر مجازی، حضور در نمایشگاهها و بازدید کارخانهها برای ارتقای دانش بهره میبریم.
بحث ارتقای کیفیت و افزایش استانداردها و الزامات خودرو، حضور خودروهای جدید و متنوع، انتظارات بالای مشتریان و بحث کنترل هزینههای تولید از مهمترین چالشهای قطعهسازان و خودروسازان است. با برقراری یک فضای مهندسی، دانشمحور و منعطف میتوان این موارد را مدیریت کرد. مشکلات مالی قطعهسازان یکی از مهمترین موانع در گسترش زیرساختهای کیفی و مهندسی در مجموعههاست. مهندس فرحبخش راهکار و استراتژی شرکت متینکیمیا برای آینده را اینگونه توصیف میکند: استراتژی این شرکت بر اساس وضعیت موجود، پیشامدهای آینده و شرایط کشور تنظیم میشود؛ در دو تا سه سال آینده باید ابتدا از وضع موجود یعنی رکود و تورم خارج شویم. استراتژی ما به این شکل است که در وهلۀ نخست قدری ماشینآلات و ابزار تولید خود را بهروز کنیم. همچنین از افراد و جوانهایی که در این زمینه دانش بیشتری نسبت به بقیه دارند استفاده کنیم و بتوانیم ابزار کنترلی و تولیدی را ارتقا دهیم؛ بهگونهای که رضایت مشتری را به همراه داشته باشد. همکاری جدید ما با شرکت کرهای به گونهای مکمل این موضوع است. به طور کلی در برنامه مدیریتی شرکت متینکیمیا همواره حدود 10 درصد از فروش سالیانه برای ارتقای مجموعه کیفیت صرف میشود.
مشکل تأمین نقدینگی و راهکارهای متینکیمیا
مدیرعامل شرکت متینکیمیا در مورد نگرانیهای به وجود آمده از خبر ورود استانداردهای 85گانه به صنعت خودرو میگوید: ممکن است جای نگرانی باشد اما وقتی دانش آن وارد شود و مطالعات لازم صورت بگیرد، جای نگرانی نیست. قطعأ ما کارشناسانی برای آموزش و برخورد با این استانداردها تربیت میکنیم. توقف تولید محصولاتی مانند پراید موجب توقف بخشی از خطوط تولید قطعات در کارخانه متینکیمیا میشود. بنابراین اولین استراتژی ما همواره این است که اگر خودرویی وارد بازار شود؛ بلافاصله در هر شرایطی طراحی و ساخت برخی قطعات خودروی جدید را در واحد مهندسیمان فعال کنیم. الان قطعات مدول کمک فنر 4مدل از خودروی SP100 را مهندسی معکوس کردهایم. نمونه اولیه این قطعات ساخته شده و اقدامات لازم جهت بحث آزمون و کنترل کیفیت آنها نیز انجام گرفته شده است. حتی برخی از آنها تأییدیه نیز گرفتهاند.
این صنعتگر بیان میکند: در این میان، عمدهترین مشکل ما در شرکت، تأمین نقدینگی است. اگر شرکتها 20درصد مطالبات ما را انجام دهند، به سرعت ماشینآلات را بهروز و آزمایشگاه را تجهیز میکنیم؛ میزان تولید و کیفیت قطعات را دستکم ۳۰ درصد افزایش میدهیم. ما اکنون ظرفیت سه شیفت داریم که تنها یک شیفت کار میکنیم.
وی در خصوص راهکارهای برونرفت از مشکلات کنونی میگوید: اگر شرکتهای زنجیره تأمین قطعات خودرو مانند سازهگستر یا ساپکو سالانه مواد خام مورد نیاز کل قطعهسازان را به صورت عمده وارد کنند، مواد موردنیازی که قطعهسازان میبایست به سختی از خارج واردکنند فراهم میشود. بخش مهمی از موضوع کیفیت در گرو مواد اولیه است. وقتی یک شرکت قطعهساز این مواد خام را از بازار فراهم کند، هم هزینه بیشتری دارد هم کیفیت آن به شدت به وضعیت بازار وابسته است. اما اگر این مواد توسط شرکتهایی مثل سازهگستر و ساپکو فراهم شود، از نظر کیفیت و قیمت شرایط مشخص و مطلوبتری خواهد داشت.
اگر مشتریان ما 20درصد مطالبات ما را پرداخت نمایند، به سرعت ماشینآلات را بهروز و آزمایشگاه را تجهیز میکنیم؛ میزان تولید و کیفیت قطعات را دستکم ۳۰ درصد افزایش میدهیم. ما اکنون ظرفیت سه شیفت داریم که تنها یک شیفت کار میکنیم. |
وی ضمن بیان توضیحاتی در اینباره که چگونه این اقدام موجب جبران نقدینگی، کاهش هزینهها، کاهش قیمت تمامشده محصول و افزایش کیفیت میشود، میافزاید: این کار کمک قابل توجهای به تولیدکننده خواهد کرد. به این طریق سازهگستر و ساپکو به جای پرداخت نقدی به شرکتهای قطعهساز، مواد خام آنها را تأمین میکنند. قیمت تمامشده برای آنها کاهش مییابد و باعث میشود مشکل کیفی به حداقل برسد.
از برنامههای آینده این شرکت رسیدن به جایگاه نخست بزرگترین تولیدکننده کلاهک در کشور و تولیدکننده متعلقات سیستم تعلیق را میتوان نام برد. آیندهای که برای شرکت متینکیمیا به عنوان شرکتی با بالاترین میزان درصد در تولید کلاهک و برخی قطعات ضربهگیر یک هدف دوردست نیست. مهندس فرحبخش در اینباره میگوید: در وضع اقتصادی فعلی تحقق این دورنما دشوار است اما تلاش کردهایم از طریق برقراری ارتباط با شرکتهای بزرگ دنیا و ارتقای دانش فنی این مهم را محقق کنیم و بتوانیم تولید قطعات تعلیقی را توسعه دهیم و برای سایر گروههای خودروسازی تولید قطعه داشته باشیم.
اما از دلایل اینکه برای محصول تولیدی آینده قطعات تعلیق را انتخاب کردیم، این است که یکی از تخصصیترین قطعات خودرو با کاربرد لاستیک و حساسیتهای بسیار بالا سیستم تعلیق آن است. این قطعه در خودرو تحت ارتعاشات زیادی قرار میگیرد و به همان نسبت باید حساسیت بالایی داشته باشد. بنابراین الزامات مشتری هم بیشتر است. برای مثال، شاید یک ضربهگیر یا یک درپوش ساده نیاز به آزمونهای پیچیده یا الزامات خاصی از طریق مشتری نداشته باشد، اما قطعأ قطعهای که بر سر کمکفنر نصب میشود شرایط و الزامات خاصی مانند فرمولاسیون لاستیک، دانش فنی آزمونها و استانداردهای جامع و ... را دارد.
مهندس فرحبخش بنیانگذار شرکت متینکیمیا صحبتهای خود را با اشاره به گسترش بازار و شروع صادرات اینگونه به پایان رساند:
اگرچه تا به حال به صورت مستقیم در امر صادرات ورود نکردهایم اما با توجه به بازار پس از فروش خوبی که برای قطعات ما وجود دارد، برنامهای برای صادرات محصولات در آینده اتخاذ شده است. در حدود 20 درصد قطعات ما دسته موتورهای کامیونهای 1921 و 1924 است که برای شرکت اپکو تولید میشود. شرکتهای کشورهای خلیج فارس مانند کویت، عراق و دیگر کشورهای شیخنشین از کامیونهای بنز بسیار استفاده میکنند. ما در صادرات دخالت مستقیم نکردیم و به طور غیرمستقیم بوده است.
او در خصوص صادرات بیان میکند: باخبر هستیم در سالهای آینده کشور تاجیکستان دو یا سه خط تولیدی برای جنرال موتور راهاندازی میکند. در نظر داریم پس از همکاری با شرکت کرهای، در این زمینه ورود کرده و صادرات محصول را دنبال کنیم.
البته محصولاتی از شرکت متینکیمیا مانند درب باک و کلاهک به صورت غیر مستقیم و توسط خودروهای ساخت داخل در سبد صادرات قرار میگیرند.
استراتژی متینکیمیا برای تداوم تولید و رضایت مشتری
«مهدی فرحبخش» رییس هیأت مدیره شرکت است. کارشناسی خود را در رشته مدیریت بازرگانی گرفته و چندین سال است که در حوزه قطعات وارداتی شرکت فعالیت میکند.
وی با اشاره به عدم وجود برخی از اقلام مورد نیاز شرکت در زمان تحریم بیان داشت: در چنین شرایطی شرکت متینکیمیا میبایست تولید را ادامه میداد از سویی رضایت مشتری را با توجه به نایاب بودنِ مواد اولیه باید جلب میکرد. این در حالی بود که برخی شرکتهای اروپایی و نیز شرکت الجی حاضر نبودند با ما قرارداد همکاری ببندند.
تحقیقاتی انجام دادیم و با شرکتهایی مانند شرکت کرهای کلون صحبت کردیم. مواد اولیه آنها را جایگزین مواد اولیه شرکتهای اروپایی کردیم که دیگر حاضر نبودند با ما قرارداد ببندند.
به گفته این صنعتگر، در زمان تحریم به جای خط کشیدن روی هزینهها، تأمینکنندههایی را پیدا کردند که مواد اولیه را با کیفیت تأمینکننده اروپایی تأمین کنند؛ مراحل تأیید مشخصات کیفی این مواد، منطبق بر استانداردها و با انجام تمام آزمونها اجرا شد.
مهندس فرحبخش با تأیید این موضوع که در زمان تحریم، پیچیدهترین فرایند تولید، تأمین مواد اولیه و ناپایداری قیمت ارز است، درباره استراتژی شرکت در آن زمان میگوید: شرکتهایی مثل شرکتهای هلندی و شرکت الجی که مواد اولیه مهم در تولید قطعات ما را به بازار جهانی وارد میکنند حاضر نبودند در زمان تحریم با ما کار کنند. بنابراین واحد بازرگانی فنی ما با حضور در نمایشگاهها، تحقیقات و مذاکرات فراوان توانست شرکت کلون را به عنوان تأمینکننده مواد اولیه باکیفیت جایگزین کند. بعد از اینکه بررسیهای لازم انجام شد مواد اولیه تأیید شد و ما آن را وارد کردیم.
این صنعتگر با بیان اینکه سایر قطعات در داخل تولید میشود و در مورد آنها با بحران روبهرو نیستیم، میگوید: برای برونرفت از نگرانیهای ناشی از تحریمها، منابع تأمین موازی ایجادکردیم. ضمن اینکه حداقل سفارش ما برای یک سال است. نقطه سفارش ما طبق دستورالعمل مدیریت کیفیت است. ذخیره احتیاطی را فوقالعاده افزایش دادیم و برای یک سال سفارش میدهیم. قرارداد را برای یک سال میبندیم چون اگر تحریم هم باشد آنها موظف هستند به مدت یک سال قطعه را برای ما تأمین کنند.
افزایش 50درصدی تولیدات، ثمره تغییر در تولید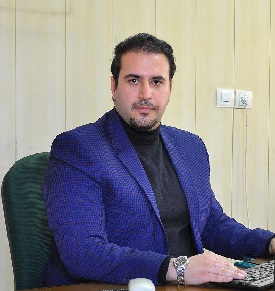
مهندس «سهراب عباسی» کارشناسی مکانیک ساخت و تولید دارد. بیش از 13 سال است بهطور مستقیم در حوزه صنعت خودرو فعال است. بیش از چهار سال است که در شرکت متینکیمیا حضور دارد.
مهندس عباسی درباره فعالیتهای خود در راستای تغییرات ایجادشده در بخش تولید، طراحی و مدیریت کیفیت میگوید: ما سیستم استاندارد کیفیت ISO/TS 16949را به صورت واقعی پیاده کرده ایم. در واقع با تصمیماتی که در زمینه مدیریت اتخاذ شد توانستیم کاهش جریان مواد در راستای کاهش قیمت تمامشده محصول را اجرا کنیم. با این کار قیمت تمامشده محصول کاهش یافت.
توانستیم کاهش جریان مواد در راستای کاهش قیمت تمامشده محصول را اجرا کنیم. با این کار قیمت تمامشده محصول کاهش یافت. |
ایشان در ادامه می افزایند: طی مدت حضور من در متینکیمیا بیش از 10 شماره فنی از سازهگستر تأییدیه گرفتیم که مشروط نبود، بلکه کامل و دائم بود. در حال حاضر در حدود ۵ قطعه شماره فنی (به جز پروژههایSP100 و مهندسی معکوس) است که در حال اخذ تأییدیه نمونه اولیه هستیم.
وی میگوید: تغییر عمدهای که در بخش تولید انجام شد استخدام پرسنل متخصص بود. در واقع شاخصههایی که در بحث تولید در استاندارد کیفیت ISO/TS 16949 مطرح میشود، مثل شاخص OEE یا شاخص درصد تحقق برنامه یا اجرایی شدن را در پیش گرفتیم. خودمان برنامهریزی تولید را انجام دادیم و طبق همان شاخصها جلو رفتیم.
ما بحث عملکرد اپراتورها، PPM تولید و ضایعات قطعه، شرایط محیطی، تجهیزات و ماشینآلات را مورد بررسی قرار میدهیم تا به بهبود شرایط تولید، کاهش MRP و افزایش ظرفیت تولید منجر شود.
وی میافزاید: با ایجاد یک تعادل در خط تولید و اضافه کردن بهینه قالبها ظرفیت تولید افزایش یافت. در طراحیهای قالبهای جدید به گونهای برنامهریزی و زمانسنجی شد که بتوان از قالبهایی با حفرههای بیشتر استفاده کرد.
افزایش ظرفیت تولید با تغییراتی در برنامهها، افزایش ماشینآلات و افزودن شیفت کاری برای پرسنل تحقق یافت. در واقع، ما با همان نیروها و اضافه کردن شیفت کاری و ارتقای تکنولوژی همراه با کاهش هزینهها این کار را انجام دادیم.
مهندس عباسی در این باره که چقدر توانستند افزایش تولید داشته باشند، بیان میکند: با همان منابع انسانی توانستیم در برخی محصولات تا ۵۰ درصد افزایش تولید داشته باشیم؛ البته میتواند بیشتر هم بشود اما قیمت تمامشده با توجه به شرایط و دستمزدها تغییر میکند.
پروژههای آینده
مدیر کارخانه متینکیمیا برنامهریزیها و تصمیمات اتخاذ شده در مورد آینده را اینگونه ترسیم میکند: همواره بحث تولید برای مدیریت بحثی تمام شده و حل شده است. اولین پروژه ما برای آینده حفظ شرایط موجود است. گام بعدی بهبود شرایط و توسعه محصولا جدید در متینکیمیاست. با توجه به تصمیمات جدید گروههای خودروسازی و حضور خودروهای جدید بزرگترین پروژه که در دست داریم تمرکز بر پروژههای SP100 است.
وی در مورد پروژه طراحی و ساخت سیستم تعلیق خودرو SP100 میگوید: با توجه به اینکه پلتفرم این خودرو به خودروی برلیانس شباهت دارد و با تجربه مشابهای که در زمینه کلاهک خودروی پراید و تیبا داشتیم، نمونه CKD آن را مهندسی معکوس کردیم.
مهندسی معکوس را از واحد R&D شروع کردیم؛ در واقع در آنالیز مواد اولیه، کشیدن نقشههای سهبعدی و طراحیهای انجامشده مشکلات و موانعی وجود داشت که در مهندسی معکوس معمولاً با این قبیل مشکلات مواجه خواهیم شد. با وجود چالشها و موانعی که وجود داشت طراحی آن صورت گرفت. واحد مهندسی شرکت متینکیمیا توانست مجموعه الزامات و آزمونهای مورد نیاز این قطعه را نیز تعریف کند. فاز بعدی، تولید قالب و قطعه بود. موفق شدیم یکی از پلتفرمهای خانواده SP100 را به تولید انبوه برسانیم.
آزمونها و اندازهگیریها
مهندس عباسی با بیان اینکه مدارک فنی و مهندسی این پروژه جدید توسط کارشناسان و مهندسی شرکت متینکیمیا تدوین شده است، میگوید: با بیش از دو دهه سابقه در زمینه آزمون قطعات مشابهای مثل کلاهک پراید، فیزیک قطعه و آنالیز مواد را انجام دادیم. با استفاده از روش آزمون و خطا، آزمونهای مقایسهای و کمکی که از دوستان و صاحبنظران گرفتیم، توانستیم برنامه آزمونهای این قطعه را تدوین کنیم. ولی هنوز نهایی نشده و در دست بررسی و تحلیل است.
ظهور یک محصول جدید در خودروسازی موجب ارتقای دانش در صنعت قطعهسازی است. باید کلیه الزامات و استانداردهای مرتبط بومیسازی و تدوین و کلیه تدابیر لازم برای پاسخگویی به آنها در نظر گرفته شود. در این راستا برنامهریزیهایی در شرکت متینکیمیا صورت گرفته است. مهندس عباسی در این باره که برای پوشش الزاماتی که در مدارک آزمون است چه تدابیری اندیشیده و تصمیم دارند در فاز توسعۀ فضای آزمایشگاه چه اقداماتی انجام دهند، بیان میکند: برای این کار افراد متخصص جذب شدهاند. طرح توسعه فضای آزمایشگاه هم از سوی مهندس فرحبخش در دستور کار قرار دارد. این برنامه به صورت جدی از سوی مدیریت ارشد حمایت میشود و در نظر است این کار در برنامهای کوتاهمدت انجام شود. اما در حال حاضر اولویت اول ما بحث طراحی، تولید و آزمون قطعات جدید مجموعه است.
به گفته این صنعتگر، تجهیزات مربوط به آزمونهای عمومی از جمله دستگاههای کشش، فشار، دوام و تجهیزات اندازهگیری ابعادی مانند CMM، انواع CFها، کولیس و میکرومتر در این مجموعه وجود دارد. آزمونها منطبق بر استانداردها و الزامات خودروسازی بوده و تجهیزات آزمایشگاهی به صورت دورهای کالیبره میشوند.
وی خاطرنشان میکند: نکتهای که شرکت متینکیمیا را نسبت به بقیه شرکتها متمایز میکند، آزمونهای خاص قطعات است. آزمونهای دوام، آزمونهای داینامیک و آزمونهای دائمی؛ این آزمونهای خاص مطابق برنامه بر روی قطعات قدیمیتر و روی قطعات جدید مثل SP100 انجام میشود.
در مورد قطعات جدید آزمونهای عمومی در آنالیز مواد و تجهیزات اندازهگیری ابعادی در مهندسی معکوس بسیار کاربردی هستند. همینطور در مورد آزمونهای خاص قطعات جدید طرح پیشنهادی خود را مطرح کردیم و منتظر نظر نهایی مشتری هستیم. متناسب با توسعه فضای آزمایشگاه و پروژههای جدید جذب و آموزش نیروی متخصص در دستورکار ما قرار دارد.
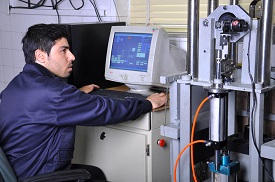
همزمان با برنامههایی که پیرامون توسعه آزمایشگاه و تجهیزات آزمون داریم کسب استاندارد ISO/IEC 17025 مدنظر است که امیدواریم طی یک سال آینده اجرایی شود.
وی درباره فعالیتهای واحد تحقیق و توسعه که زیرنظر مدیریت کارخانه است، توضیح میدهد: طبق استاندارد ISO/TS 16949 نقشهای برای توسعه داریم که تمام فرآیندهای شرکت در آن مشخص شده است. یکی از این فرایندها بخش مهندسی و R&D شرکت است که با در نظر گرفتن کلیه ورودیها، خروجیها و شاخصها کار تکوین محصول نهایی را انجام میدهد.
او میافزاید: ما طراحی DFMEA را انجام نمیدهیم اما طراحی PFMEA را انجام میدهیم. کلیه طراحیها با توجه به الزامات SQL، SPASS و یا هر الزام دیگری که مد نظر مشتری است انجام میشود. تکوین محصول را کاملاً از صفر تا صد انجام میدهیم. به این صورت که ابتدا مهندسی معکوس انجام میشود؛ نقشههای فنی، مدارک مهندسی و برنامههای آزمونها حاضر میشود؛ پس از آن به واحد تولید تحویل میشود. تمام این موارد با نظارت واحد کنترل کیفیت انجام میشود.
وی درباره چگونگی بهروزرسانی مدارک و اعتباردهی میگوید: با توجه به اینکه مشتری نقشههای مهندسی و برنامه آزمونها را تعریف میکند، ما نیز موظف هستیم تکوین محصول را طبق همان نقشه انجام دهیم. اگر در جایی تغییر طرح و تغییر مواد اولیه یا تغییر محصول داشته باشیم، موظفیم به تأیید مشتری برسانیم. علاوه بر این موضوع کلیه سوابق مشکلات کیفی و تغییراتی که در الزامات مهندسی قطعه رخ میدهد نیز باید به تأیید مشتری برسد.
مهندس عباسی در مورد مهمترین اقداماتی که تاکنون برای افزایش کیفیت، افزایش تولید و رضایت مشتری انجام دادهاند، میگوید: مهمترین اقداماتی که در دو سه سال اخیر انجام دادیم اخذ تأییدیههای مختلف کیفی بوده است. افزایش میزان تولید تا 50 درصد، ثبات قیمت محصول که با توجه به تورم؛ در واقع، کاهش قیمت محسوب میشود از دیگر گامهایی است که در جهت افزایش رضایت مشتری برداشته شده است. چهار سال است که قراردادهای ما افزایش نیافته است. در حالیکه بسیاری از شرکتها و همکاران ما قیمت قطعات را افزایش دادند، اما ما با پایینآوردن قیمت تمامشده محصولات کاری کردیم که نیاز به افزایش قیمت نباشد. از اقدامات مثبتی که در این دوره انجام شد، تغییر ساعت کاری بود که در کاهش هزینهها تأثیر چشمگیری داشت؛ اضافهکاری را فقط در گلوگاهها داشتیم، با چند ساعت اضافهکاری افزایش ظرفیت تولید ایجاد کردیم که این هم در کاهش هزینه قیمت تمامشده مؤثر بود.
در چند سال اخیر در مورد کاهش ضایعات، تحلیلها و فعالیتهای بسیاری انجام شد و کاهش ضایعات بسیار خوبی داشتیم. PPM خارجی شرکت که صفر است اما در مورد PPM داخلی هم به موفقیتهای خوبی رسیدیم.
در مجموع، درصد بالای تحقق برنامههای تولید، کاهش جریان مواد و افزایش بازده اپراتوری باعث شد کاهش هزینه داشته باشیم. هزینههای کیفی مانند هزینه بازرسی را نیز از طریق خودبازرس شدنِ قطعات کاهش دادیم.
در چند سال اخیر در مورد شاخص میزان ضایعات، تحلیلها و فعالیتهای بسیاری انجام شد و در نتیجه آن کاهش ضایعات به پایینترین حد خود رسیده است. میزان برگشتی مشتری (PPM) خارجی شرکت نیز صفر است. |
وی در خصوص رضایتمندی مشتری میگوید: ما افزایش رضایتمندی مشتری را داشتیم. تاکنون هیچ شکایتی نداشتیم. دو شاخص سنجش عملکرد و تحویل به موقع از مهمترین معیارها در تخمین میزان رضایت مشتری است. درصد سنجش عملکرد هم که به 3 یا 4عامل برمیگردد؛ تحویل به موقع، PPM محصول و اقدامات اصلاحی؛ طبق نظام ISO/TS 16949 و شاخصهای داخلی که ارزیابی میکنیم، در هر یک از این موارد، شاخصهایی که سایت ما از سوی مشتری اعلام میکند بیش از 85درصد است.
وی در تشریح عملکرد واحد مهندسی بیان داشت: واحد مهندسی در حال حاضر و با توجه به شرایط موجود با سرپرستی مهندس قزاقی و مهندس کیوان متین فعالیت دارد. درصدد هستیم که با توسعه ساختار سختافزاری و دانش فنی، در زمینه طراحی قالب با نقشههای سهبعدی و فیکسچرهای کنترلی کار خود را توسعه دهیم.
فعالیتهای شرکت متینکیمیا فقط به قطعات لاستیکی محدود نشده و واحد فلزکاری نیز در این شرکت وجود دارد که شامل: پرسهای هیدرولیک سنگین، پرسهای ضربهای سنگین، پرسهای کوچک، نقطهجوش، خط شستوشوی فلز و خط شاتپلاس است.
در حال حاضر 20 تا 25 درصد ظرفیت فلزکاری در شرکت متینکیمیا به منظور تأمین نیازهای خطوط تولید فعال است. توسعه فلزکاری در این شرکت از برنامههای آینده است. مهندس عباسی تصریح میکند: اگر قطعهای از نظر استراتژی برای شرکت بهینه و بهصرفه باشد، با توجه به ظرفیت خالی موجود، برای تولید استقبال میکنیم زیرا ما توانایی فنی و تخصص لازم آن را داریم.
وی درباره دیگر واحدهای شرکت میگوید: واحد چسبکاری که فقط مربوط به قطعات لاستیک است و یک واحد مجزاست و واحد موادسازی که شامل کلیه تجهیزات لازم است؛ بهگونهای که دیگر نیاز نداریم خدمات بمبوری و از این دست خدمات را از بیرون دریافت کنیم.
وی خط تولید را شامل پرسهای متنوع و پرس پخت عنوان میکند و میافزاید: تنوع بالایی در قطعات پرسکاری داریم. پرسهای معمولی تماماتوماتیک و نیمهاتوماتیک، پرس پخت تزریقی و پرس پخت وکیوم که برای قطعات خاص استفاده میشوند. پرسهای پخت وکیوم تحت خلأ قطعه را تولید میکنند و برای تولید قطعاتی با جداره نازک و بدون عیوب ظاهری و حفره مناسب است.
خط مونتاژ شامل قسمتهای مختلف مونتاژ، پرسهای کوبش و قسمت پیچ کوبی است؛ البته در تمامی واحدها بخش کنترل هم داریم. در فلزکاری فیکسچرهای کنترلی و واحد موادسازی رئومترها برای کنترل ترکیبات مواد وجود دارد. یک خط رنگ الکترواستاتیک هم داریم که استاندارد است و کیفیت رنگ محصول را تضمین میکند.
همواره سعی شده است شاخصهای استاندارد ISO/TS 16949 را در تمام بخشها پیادهسازی کنیم. آخرین واحد، تعمیرات و نگهداری است که بر طبق این استاندارد دو شاخص دارد؛ شاخص میانگین فاصله بین تعمیرات و نگهداریها و خود فاصله زمانی تعمیرات و نگهداریها. بررسی این دو شاخص به عنوان ابزاری برای افزایش بازده عملکرد شرکت متینکیمیاست.