مهندس امیر خرسندیطلب؛
قائممقام مدیر عامل و مدیر کارخانه و شرکت بهسوز خودرو آبی
انجام آزمونهای حین
تولید و آزمایشگاهی
مهمترین مزیت رقابتی
در شرکت
بهسوز خودرو آبی
تولید گاردان فرایند چندان دشواری نیست، ولی انجام فرایندهای آزمون گاردان بسیار مهم و پیچیده است. به جرات میتوان گفت که در شرکت بهسوز خودروی آبی، ایستگاههای آزمون اهمیت بیشتری از خود فرایند تولید گاردان دارند.
جناب مهندس با سپاس از وقتی که در اختیار نشریه ما قرار دادید، لطفاً در ابتدای گفتگو مختصری راجع به تاریخچه شرکت "بهسوز خودرو آبی" بفرمایید.
شرکت بهسوز خودروآبی با ساخت کیت کامل تجهیزات الکتریکی سوخت گاز مایع (LPG) برای خودروهای گازسوز فعالیت خود را آغاز کرد. پس از مدتی تولید این محصول ممنوع شد و در نتیجه، شرکت به تولید قطعات خودرو پرداخت. در ابتدا به عنوان تامینکننده اصلیِ شرکت "سردساز خودرو" تولید قطعات متعلق به کولر خودرو از قبیل انواع کندانسور، قاب فن، خشککن، پایهها واتصالات کندانسور در دستور کار این شرکت قرار گرفت.
پس از مدتی با تولید ترمز درب پراید در رده قطعهسازان همکار شرکت خودروسازی سایپا و گروه سازهگستر قرار گرفتیم و تولید قطعات دیگر همانند براکت صندلی و اگزوز، بست نگهدارنده اگزوز، تراورس و دیگر قطعات پرسکاری نیز در دستور کار شرکت قرار گرفت. از حدود سه سال پیش، کارخانه جدید شرکت در شهرک صنعتی هشتگرد برای تولید مجموعه گاردان راهاندازی شد. پس از آن طی انعقاد قراردادی، با تولید همین محصولِ گاردان برای خودروسازهای زامیاد و گروه بهمن، پروژه¬های تولیدی شرکت گسترش یافت.
با توجه به اهمیت نقش چارت سازمانی در تسریع روند کارها و توسعه سازمان یافته، لطفاً ساختار شرکت خود را تبیین فرمایید.
در چارت سازمانی شرکت بهسوز خودرو آبی، پس از هیات مدیره و مدیرعامل واحدهای بازرگانی، طراحی مهندسی، تضمین وکنترل کیفیت و واحد اداری و مالی قرار دارند. لازم به ذکر است واحد طراحی مهندسی شامل دو بخش تولید و مهندسی محصول است. بنده نیز به عنوان قائم مقام مدیر عامل و مدیر کارخانه در شرکت مشغول به کار هستم. بخش مهندسی تولید وظایف تحقیق وتوسعه (R&D) را نیز بر عهده دارد؛ این تیم در حال حاضر در زمینه بهینهسازی فیکسچرها واصلاح آنها و همچنین اصلاح فرایند تولید، طراحی محصول و تجهیزات فعالیت دارد.
مهمترین محصول شرکت در حال حاضر، گاردان انواع خودرو است. تکنولوژی، خطوط تولید و تجهیزات آزمایشگاه گاردان از شرکت روبات ماشین خریداری شده و سپس کارشناسان و تکنسینهای ماهر نیز به شرکت بهسوز خودرو پیوستند. پس از بازنگری و بهینهسازی تجهیزات و فرآیندها، این شرکت توانست میزان تولید و کیفیت محصولات خود را افزایش دهد، به گونهای که از آذرماه سال 1392 با هماهنگی شرکت سازهگستر سایپا جهت رفع نیاز خودروساز، تولید این شرکت افزایش قابل توجهی یافت. به موازات افزایش تولید با بهرهگیری از بدنه کارشناسی مجرب و استفاده از استانداردهای جدید، نسبت به ارتقای سطح کیفی و عملکرد تجهیزات اقدام نمودیم.
برای بهسازی خط و رسیدن به جایگاه کنونی، تلاش زیادی نیاز بود. یک گروه مهندسی به موازات بخش تولید به بازنگری طرحها و بررسی فناوریهای جدید پرداخت، که در نتیجه، روشهای پیشین اصلاح شد. از آنجا که، ما منبع اصلی تامین گروه زامیاد بودیم، برای پیشگیری از توقف خط در حین تولید، گروهی نیز در بخش تغییر و بازنگری فرایندها گماشته شد. در نتیجه این اقدامات، در سال 1392، تغییرات اعمال گردید و تولید به شیوه جدید آغاز شد.
از سال 1393 گروه ویژهای برای تقویت خدمات پس از فروش و برنامهریزیهای مرتبط به کار گرفته شد. در اولین گام، شیوه خرید قطعات استاندارد تغییر یافت. مثلاً برخی ویژگیهای قطعه وارداتی بلبرینگ را چنان تغییر دادیم که بتواند پاسخگوی دوره گارانتی مورد نظر قطعه باشد؛ پس از آن روی چهارشاخه تمرکز کردیم. به این منظور برند جدیدی یافته و آرم شرکت را روی آن برند حک کردیم.
در حال حاضر تولیدکننده چهار نوع گاردان هستیم. اولین نمونه مختص نیسان است وپس از آن سه تیپ مزدا OHVG که به اسم کارا شناخته می شود، مدل DAE و سواریهای مزدا را میتوان نام برد.
در سه تیپ محصول مزدا، حجم موتور 1700، 1800 و 2000 سیسی است. نوع 2000 سیسی مربوط به موتور مزداست. نوع 1800 سیسی موتور جدیدی است که با گیربکس اشاز چین وارد و DAE نامیده میشود؛ یعنی موتور و گیربکس چینی بر روی اتاق مزدا نصب میشود. در OHVG موتورهای پیکان بر روی اتاقهای مزدا نصب وبا نام کارا شناخته میشود و حجم موتور 1700 سیسی است.
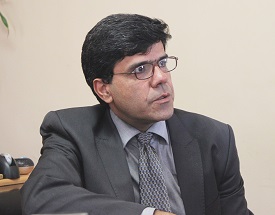
لطفاً تفاوت مشخصات گاردان، در چهار محصولی که نام بردید را ذکر فرمایید.
نخستین تفاوت، مربوط به قطر است. اول قطر و نوع مدول هزار خاری کشوهای درگیر، دوم قطر لولهها و سوم که مهمترین تفاوت است، نوع اتصالات مانند فلنج و یوک بال. تفاوت دیگر به خاطر تغییر گیربکسهاست، به این معنا که طول لوله در مدلهای گوناگون متفاوت میشود. اختلاف عمده بر سر بحث هندسی است. با تغییر قطر، توان قابل تحمل موتور نیز تغییر میکند. توضیح اینکه؛ در DAE گاردان قویتر از نوع کارا است. برای DAE با همکاری گروه مزدا از قطعات نیسانی استفاده کردیم که توان و کوپل بیشتری را تحمل می-کند. مخصوصاً در یوک بالا و فلنچ ها، همه قطعات قویتر شدند. در مزدا این قطعات ظریفتر هستند.
در OHVG هم تغییراتی انجام شد. مزدا و OHVG تقریباً مشابهاند و فقط در طول اختلاف دارند و از لحاظ هندسی نیز متفاوتاند.
طراحی تغییراتی که در هر محصول باید انجام شود، در کجا انجام میگردد؟
هر خودروساز واحد مستقل تحقیق وتوسعه (R&D) دارد که برروی طرح کار میکنند. طراحی محصول متعلق به شرکت سفارشدهنده است. مشتری بر اساس نیاز خود، مستنداتی شامل نقشههای فنی، مدارک، استانداردها و مشخصههای آزمون را در اختیار ما میگذارد و ما بر اساس این مدارک فنی، قطعات را تولید میکنیم. بدیهی است، اگر در حین تولید به مشکلی بر بخوریم که نیاز به همفکری باشد، راهکارهایی ارائه میکنیم که پس از دریافت تایید از مشتری اجرایی میشود.
به عبارت دیگر، معنی گفته شما این است که هیچ تغییری از نظر طراحی در شرکت بهسوز خودرو انجام نمیشود؟
خیر؛ ما مجاز به تغییر طرح نیستیم. تنها مورد استثنا، DAE است که در تغییرات آن با مشتری همکاری داشتیم. الزام مشتری، بالارفتن توان موتور بود. گاردانی میخواستند که توانایی تحمل گشتاور خروجی گیربکس جدید را داشته باشد. از آنجا که قطعات مزدایی نامناسب بود، از ما خواسته شد تغییراتی بر روی گاردان قبلی اعمال شود تا قادر به انتقال این گشتاور باشد.
ما طرحی پیشنهاد دادیم، شبیهسازی کردیم و نمونه را ساختیم؛ اما باز هم به ویژه برای محاسبه قطر لوله، با تیم مهندسی مشتری تبادل اطلاعات داشتیم. ضخامت و قطر لوله از پارامترهای اصلی گاردان برای تحمل گشتاورمورد نظر است. پس از ارائه پیشنهاد ما، کارشناسان مشتری آن را بررسی و صحهگذاری کردند و سپس ما بر همین اساس نمونهسازی کردیم. معنی این گفته این است که محاسبه اولیه به عهده ما بود، ولی دادههای پایهای اصلی برای خروجی گیربکس، مثل مشخصات گیربکس و توان خروجی را مشتری به ما داد. با محاسبات ریاضی و به صورت نظری اندازه حداقل قطر لوله را محاسبه نموده و سپس نزدیکترین لوله موجود در بازار را درنظر گرفتیم. یک درجه بالاتر از آن را انتخاب و نمونهای تولید کردیم و پس از تایید نهایی به تولید انبوه رسیدیم.
اگر ممکن است مراحل اخذ تاییدیه از مشتری و آزمون¬های مورد نیاز را بیان فرمایید.
گروه بهمن مشخصات آزمون (test plan) ویژهای از قبیل؛ آزمون جاده، آزمون وزن و آزمون بار دارد. اگر محصول این آزمونها را برآورده نکند، تاییدیه قطعه صادر نمیشود. پس از ساخت، نمونه در شرایط سخت در جاده آزموده میشود و شرایطی همانند آزمون در جاده کفی، جاده صعبالعبور، شرایط سخت و میزان بار اعمال میگردد. در آزمون بار وزنههای سُربی روی خودرو تعبیه میشود تا مسافتی را با این بار طی کند.
در شرکت بهسوز خودرو آبی کل مجموعه و قطعات منفصله تولید میشود؟ یا واردات قطعه هم دارید؟
قطعاتی مانند بلبرینگ و چهارشاخه وارداتی هستند، ولی قطعات فورج داخلی هستند. شرکتی که خط تولید آن توسط شرکت بهسوز خودرو خریداری شد، پیش از این با سازندگان قطعات فورج داخلی در ارتباط بود، ولی کیفیت و نوع کار باعث شد که با برندهای جدید هم قرارداد ببندیم. در این راستا با منابعی مانند شرکت توس فورجینگ که مورد تایید سازهگستر بوده و سطح کیفی بالاتری دارد وارد مذاکره شدیم و قرارداد بستیم. با تغییر پیمانکاران قطعات فورج، هزینه تولید در شرکت بهسوز خودرو افزایش یافت، ولی کیفیت کار مطلوبتر شد و ضایعات کمتر گردید. در سال جاری چهارشاخههایمان از نوع GMB وساخت ژاپن است.
آیا تصمیم ندارید که تحت لیسانس تولید کنید و در این زمینه به خودکفایی برسید؟
فرایند تولید چهارشاخه هزینهبر است و با شمارگان تولید بیست هزار و سی هزار قطعه در ماه، نمیتوان هزینهها را جبران نمود و باید بالای سیصد هزار یا حتی پانصد هزار عدد باشد. به همین سبب تلاش کردیم منبعی بیابیم که کیفیت و کلاس بالاتری در جهان داشته باشد. با شرکت ZQ چین هم مذاکره کردیم. اینها دو برند معروف جهانی هستند. شرکت GMB هم بسیار معروف است و یک منبع جهانی است که به اروپا و آمریکا هم قطعه میدهد.
با چه پیمانکارانی در داخل کشور برای تولید چهارشاخه کار میکنید؟
ما عمدتاً با شرکت "حرکتسازان توس" کار میکنیم. در این شرکت انواع و اقسام چهارشاخهها تولید یا به صورت اسمبلی وارد و در اینجا مونتاژ میشود. یکی از برندهای شرکت حرکتسازان توس PLP بوده و همچنین وارد کننده GMB هم هستند و کیفیت کارشان نیز مناسب است.
جناب مهندس، پیش از این فرمودید بلبرینگ قطعهای وارداتی است. آیا جز بلبرینگ و چهارشاخه تمام قطعات منفصله دیگر تولید داخل است؟
بله؛ صد در صد محصول در داخل تولید میشود. قطعات فورج را از پیمانکار میخریم و لولهها از لوله دقیق کاوه و ساوه تهیه میشود، لوله دقیق کاوه برای ما لولهها را در اندازه مورد نظر تهیه و به اصطلاح سایز میکند. لازم به ذکر است، پیش از این در یک مقطع زمانی لولهها را از ترکیه وارد میکردیم.
شما به منظور آزمون قطعات ورودی از چه تجهیزاتی استفاده میکنید؟ چهارشاخه و بلبرینگ آزمونهای پیچیدهای دارند.
بنا بر مشخصههای آزمون قطعه، دستگاههایی برای آزمون گاردان داریم. این دستگاهها شامل آزمون دوام، آزمون ضربه و آزمونهای دینامیکی؛ همانند دوام آب و گلولای و آزمون دور بالا میشوند. این تجهیزات برای آزمون نهایی و کل مجموعه گاردان است. وقتی قطعات استاندارد مانند بلبرینگ وارد میشود، یک نمونه گاردان، مونتاژ و بلبرینگ در جای خود قرار میگیرد و سپس با دستگاههای یادشده آزمونهای گوناگون بر روی گاردان انجام میشود.
جهت کنترل ورودی چهارشاخه نیز به به همین ترتیب عمل میکنیم. دو دست کامل چهارشاخه به طور تصادفی برداشته میشود و با آن گاردان ساخته میشود. سپس بدون انجام فرایند نهایی گاردان، آزمونهای گل و لای، دور بالا، ضربه و دوام بر روی این قطعه انجام میشود. در صورت مناسب بودن نتایجِ آزمونهای یادشده، تاییدیه ورود به انبار برای چهار شاخه صادر میگردد.
آیا در حال حاضر تجهیزات آزمون یاد شده تایید مشتری را دارد؟
بله؛ پس از بررسی توسط واحد متد سازهگستر، همه دستگاهها تایید شدهاند و کارشناسان گروه بهمن هم گزارش واحد متد سازهگستر را پذیرفتهاند. در گروه بهمن مانند شرکت سازهگستر واحد مستقلی به منظور تایید دستگاههای آزمون وجود ندارد، از این رو پس از ارائه گزارش واحد متد سازهگستر و بررسی و اجماع کارشناسان مهندسی و تامین و بر مبنای دانش و تواناییهای ایشان، صحهگذاری دستگاههای آزمون انجام شد. به شرکت ساپکو هم اعلام آمادگی کردهایم ولی بنا به منسوخ شدن خط تولید پیکان، فعلاً پیگیری نمیکنیم.
جناب مهندس، آیا با سایر خودروسازان نیز در راستای تولید گاردان همکاری دارید؟
به تازگی با واحد بازرگانی تراکتورسازی وارد مذاکره شدهایم. نیاز ایشان گاردانهای انتقال نیرو برای اکسل جلوی تراکتور است که البته در حال حاضر در مرحله مذاکرات بازرگانی هستیم. در گروه بهمن، نمونهای برای وانت کاپرا دریافت کردهایم که کارشناسان ما در حال کار بر روی آن هستند و جزو پروژههای پیشفرض ما در آینده است. همچنین از شرکت پارسخودرو برای تولید محصول جدید، ریچ، پیشنهادی داشتیم. این خودرو، نوعی وانت دو کابینه جدید چینی است که در خط پارس خودرو مونتاژ و تولید میشود. قصد دارند گاردان آن را تولید داخل نمایند. نمونه اولیه ما جهت آزمون مونتاژ پذیری ساخته و تحویل شده است.
هدف نهایی شرکت این است که در زمینه گاردانسازی به ویژه در کلاس خودروهای سواری، برند مطرحی شویم. همچنین برنامه صادرات گاردان در برنامه آتی شرکت قرار دارد؛ در این زمینه واحد بازرگانی تمهیداتی اندیشیده و زمینهچینی کار به گونهای است که پس از آنکه در تامین قطعات برای خودروسازان داخلی به حد اشباع برسیم به سوی تولید گاردان برای شرکتهای خارجی خواهیم رفت.
آیا برای توسعه صادرات اقدام عملی هم انجام شده است؟
بله؛ اخیراً بازدید و مذاکره با یک شرکت آلمانی انجام شده است. این شرکت تولیدکننده گاردانهای خط تولید برای صنایع نورد، پروفیل و لوله است، در حقیقت فرایند انتقال نیرو و سیستمهای حمل به وسیله گاردان انجام میشود. امیدوار هستیم به نتایج خوبی برسیم.
به نکته خوبی اشاره فرمودید. از آنجا که گاردان در واقع یک سیستم کوپلینگ دوار انتقال قدرت است، زمینه کاربرد آن بسیار گسترده و فراتر از خودرو است. آیا شما در داخل کشور هم فقط با خودروسازی کار میکنید یا در زمینههای دیگر نیز فعالیت دارید؟
خیر؛ ما فقط در صنعت خودروسازی فعالیت داریم. البته در یک مورد، در زمینه تجهیزات آتشنشانی کار کردیم که باز در ردیف خودرو قرار میگیرد. همچنین برای نازلهای پاشش و خاموش کنندههای سرچاهی برای شرکت نفت که با یک مفصل متحرک کار میکنند نیز کارهایی در شرکت ما انجام شده است. یکی از اهداف شرکت این است که در زمینه تولید گاردان برای صنایع غیر خودرویی نیز وارد شویم.
در سال جاری اولویت ما اتمام کارخانه جدید است وهمه طرحها به زمان تکمیل ساختار و تشکیلات جدید موکول میشود. سه سایت در جاهای مختلف داریم که قرار است در یک جا تجمیع شوند. کارخانه، 4000 متر مربع زیر بنا دارد که حدود 2300 متر به سالن تولید اختصاص داده شده است.
در حال حاضر در مرحله طراحی برای چیدمان دستگاهها هستیم. ابتدا باید فونداسیون پرسها ریخته شود. هر یک از آنها فونداسیون خاص خود را دارند. پرسهای سنگین هیدرولیکی و ضربهای، نیاز به چاله پرس دارند. طبق برنامهریزیهای انجام شده، تا پایان سال جاری حداقل فاز اول واحد پرس کاری، انتقال یابد.
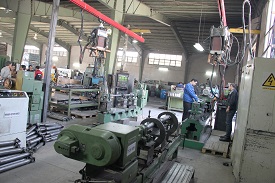
جناب مهندس خرسندی، لطفاً درباره آزمونهایی که بر روی قطعات فورج انجام میدهید توضیح فرمایید.
انواع گوناگون آزمون بر روی قطعات انجام میشود. در آزمون ضربه، یک وزنه که با نیروی گرانش زمین کار میکند، به صورت سقوط آزاد بر روی قطعه تحت آزمون رها میشود تا ضربه لحظهای به قطعه اعمال شود. دستگاه آزمون دوام، هیدرولیکی است. در آزمون آب و گل، در دور چهار هزار دور بر دقیقه آب و گل و لای بر روی قطعه پاشیده میشود. همانگونه که پیشتر اشاره شد از این آزمون، بیشتر برای بررسی کیفی بلبرینگ و چهارشاخهها استفاده میکنیم. آزمونهای ساده دیگری نیز در شرکت داریم. در یک آزمون زاویه پیچش مفصل گاردان اندازهگیری میشود. از نظر کیفی قطعات دو کله، نباید بیش از حد پیچیده شده باشد. به عبارت دیگر، نباید در قطعه انرژی پسماند داشته باشیم. چهار دستگاه آزمون بالانس هم داریم. یکی از آنها هنوز عملیاتی نشده، دیگری مخصوص گروه مزداست و دو دستگاه بزرگ نیز مختص آزمون گاردانهای تولیدی برای نیسان است. یکی از آنها برند معروف شنک آلمان و دیگری ساخت داخل است. بنا به اهمیت ویژهای که از ابتدا به مفاهیم کیفی داشتهایم، به دنبال توسعه آزمایشگاه و در نتیجه خرید تجهیزات آزمون بیشتر هستیم. هنوز با هیچ شرکتی در این زمینه به توافق نرسیدهایم.
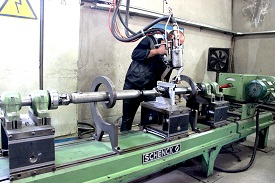 |
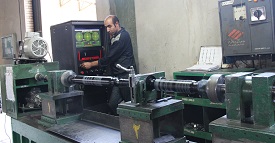 |
تجهیزات آزمون آنبالانسی میل گاردان نیسان مستقر در خطوط تولید شرکت بهسوز خودرو آبی جهت تست صددرصد قطعات |
پرهزینهترین وپیچیدهترین آزمونهای خودرویی، مثل آزمون دوام و نابالانسی بر روی گاردان انجام میشود. لطفاً در ادامه پرسش فوق، برنامه توسعه آزمایشگاه را بیشتر برای خوانندگان محترم نشریه تبیین بفرمایید.
شرکت بهسوز خودرو آبی، تنها شرکتی است که از چهار دستگاه آزمون بالانس استفاده مینماید. میدانید که هر کدام هزینههای خاص خود را دارند. همچنین ما هفت دستگاه برای انجام آزمون دوام و شش دستگاه آزمون تخریبی داریم. در صنایع کشور این بینظیر است و شاید خودروسازان هم این تعداد دستگاه را به صورت متمرکز در یکجا نداشته باشند.
اکنون همانگونه که پیشتر اشاره شد، در نظر داریم آزمایشگاه را بهروز و بهینه کنیم. فضایی که در ساختمان جدید برای آزمایشگاه در نظر گرفته و طراحی شده است، حدود 240 متر مربع است. همچنین در آینده نزدیک در راستای اخذ استاندارد ایزو 17025 نیز اقدام خواهیم کرد و بنا داریم به دیگر صنایع هم خدمات آزمایشگاهی ارائه نماییم. هم اکنون نیز قطعاتی از صنایع نظامی برای آزمون به ما ارجاع میشود. بنابراین در جهت توسعه آزمایشگاه و تبدیل به مرجعی برای انجام آزمون قطعات، هدفگذاری انجام شده و بسیار در این زمینه مصمم هستیم.
با توجه به توانمندی شرکتهای دانشبنیان سازنده تجهیزات آزمون داخل کشور، چرا از سازندههای داخلی استفاده نمیکنید؟
در زمینه دستگاههای آزمون بالانس، سازندههای داخلی خوبی داریم. با چند سازنده هم کار کردهایم؛ ولی دستگاههای آزمون مورد نیاز دیگر، ظرافتهای خاصی دارند. این تجهیزات باید منطبق بر مدارک فنی باشند و خواستههای استاندارد را پوشش دهند. این الزامات کار را کمی دشوار میکند. ما در شرکت بهسوز خودرو آبی ترجیح میدهیم بیشتر هزینه کنیم و با اطمینان دستگاههای آزمون را تهیه نماییم. افرادی مانند آقای دکتر فرزانه، آقای مهندس احمدی و دیگران هستند که میتوانند دستگاه را طبق مشخصات مورد نیاز طراحی نموده و بسازند؛ ولی ما نمیخواهیم زمانی که دستگاه آماده وجود دارد به آزمون وخطا بپردازیم. چهار دستگاه نیاز داریم. این احتمال وجود دارد که یکی از آنها را از شرکتهای داخلی تهیه نماییم.
شما در شرکت در زمینه تولید گاردان به شکل تخصصی کار کردهاید. پس از گاردان مهمترین محصول شرکت شما چیست؟
بعد از گاردان، مهمترین قطعه تولید شده در شرکت، ترمز درب تیبا و پراید است که تامینکننده اصلی این قطعات شرکت ماست. ما بر روی تولید ترمز درب تمرکز کردهایم و حتی برای سایر خودروها هم برنامه داریم. لازم به ذکر است در زمینه صادرات ترمز درب در شرکت ما فعالیتهایی انجام شده و مذاکراتی با شرکتهای هیوندا، تویوتا و پژو داشتهایم ودر مرحله نمونهسازی هستیم.
علاوه بر گاردان و ترمز درب، یازده قطعه دیگر مانند تراورس عرضی پراید، براکت صندلی، براکت تقویتی دو مهره و.... نیز در شرکت بهسوز خودرو تولید میشود.
نقطه قوت بهسوز خودرو آبی نسبت به دیگر رقبا چیست؟ بر روی کدام ویژگی بیشتر میتوانید تاکید نمایید؟
به نظر اینجانب، سرعت عمل وکیفیت بالای انجام کارها بزرگترین نقطه قوت در شرکت ماست. ما توانایی تولید یک محصول در کوتاهترین زمان ممکن را داریم. گاهی سفارش دریافتی به گونهای است که نیاز به تغییر دارد. در کمترین زمان تغییرات اعمال شده و قطعه تحویل مشتری میشود.
شیوه طراحی این تغییرات چگونه است و این فرایند توسط کدام بخش انجام میشود؟
شخص آقای مهندس نوری، مدیر عامل شرکت، در راس تیم طراحی قرار دارند. علاوه بر ایشان، بنده و دوستانی که تازه به گروه طراحی شرکت پیوستهاند، ایشان را همراهی میکنیم. کار تحقیق وتوسعه به عهده تیم ماست، ولی از آنجا که حجم کار بسیار بالاست، به ناچار از نفرات و شرکتهای بیرون از شرکت نیز خدمات دریافت میشود و با جاهای مختلف کار میکنیم. انجام طراحی در بعضی قسمتها به پیمانکار سفارش داده میشود و در آینده در صدد آن هستیم که بخش تحقیق وتوسعه مستقلی داشته باشیم.
آزمایشگاه و تجهیزات آزمون دو نقش عمده در تولید میتواند داشته باشد. از یک سو، تامین کننده نیازهای R&D و مهندسی است. زمانی که یک محصول طراحی میشود، نتایج طراحی با آزمودن آشکار میشود و مهندس طراح بر اساس این نتایج میتواند طرح خود را توسعه دهد و اصلاح کند. از سوی دیگر، میتواند باعث رضایت مشتری و افزایش کیفیت و کاهش ضایعات شود. به سخن دیگر، هرچقدر شرکتی در حوزه آزمون قویتر باشد و آزمایشگاه مناسبتری داشته باشد، به همان نسبت کیفیت قطعات تولیدی، بهتر میشود و در خدمات پس از فروش نیز شاهد قطعات برگشتی کمتری خواهیم بود. آیا تجهیزات آزمون استفاده شده در شرکت بهسوز خودرو این دو آورده را برای شما به همراه داشتهاند؟
در تایید گفتههای شما، عرض میکنم که، بدیهی است نتیجه آزمون در کیفیت محصول اثر گذار است. قطعهای مانند گاردان آزمونهای بسیار مهمی دارد و از سوی دیگر در انتهای خط، آزمون صد در صد داریم. ما بنا به کمیت و کیفیت مناسب تجهیزات آزمونی که در اختیار داریم، در خدمات پس از فروش، کاهش معناداری در برگشتیها داشتهایم که مستقیماً مربوط به آزمایشگاه وتجهیزات آزمون است.
ما سختگیری و کنترل شدیدی بر روی مراحل مختلف تولید و بازرسیهای کیفی داریم. در آخرین ایستگاه یعنی در مرحله بالانس، آزمون run out دوباره انجام و این پارامتر مهم کنترل میشود. این ایستگاه، گلوگاه تولید است و در تولید سکتهای ایجاد مینماید که باعث کاهش آمار تولید میشود؛ ولی بنا به اهمیت چک کردن پارامترهای تاثیرگذار بر روی کیفیت گاردان ما این هزینه را پذیرفتهایم.
در نتیجه صرف زمان و هزینه بیشتر، ما شاهد افزایش رضایت مشتریان هستیم. گروه بهمن نمونه بارز یکی از مشتریانی است که در گزارش سال پیش رضایتمندی خود را از گاردان گروه بهسوز خودرو اعلام نمودند. در این شرکت برای خدمات پس از فروش در تعمیرگاهها از گاردان ما استفاده می نمایند. این نکته نمایانگر میزان بالای رضایت خدمات پس از فروش در شرکتهای خودروساز است.
در گذشته تعداد زیادی از برگشتی قطعات گاردان، به خاطر نقص بلبرینگ وچهارشاخه بود که با انجام کنترل های ورودی به کمک دستگاههای آزمون دوام و گل و لای و ... بسیار کاهش یافته است.
در سیستم کنترل ورودی، بر روی این دو قطعه آزمونهایی انجام میشود. در ابتدا نیز از بین حدود هشت برند، با انجام آزمونهای گوناگون یکی از شرکتها که قطعات با کیفیت بالاتری تولید مینمود را انتخاب کردیم. با آزمودن قطعه در آزمونهای یاد شده در صورتی که قطعه در شرایط دوام و گل و لای زنگ نزند، دمونتاژ نشود یا گیرپاژ نکند، از کیفیت قطعه اطمینان مییابیم. تغییراتی نیز در دستگاههای آزمون دادهایم تا بتوان هر سه نوع گاردان مزدا، DAE و نیسان را با آنها آزمود.
آقای مهندس، انواع آزمونهایی که در خط تولید یا آزمایشگاه انجام میشوند کدامند؟
یک دستگاه آزمون ضربه داریم که در دو وضعیت استاتیکی و سقوط آزاد کار میکند. بر اساس استاندارد تعریفشده یک وزن خاص، حدود 270 کیلو گرم، حول محوری گشتاور ایجاد میکند. دستگاه، ضامن مکانیکی و یک جک هیدرولیک دارد.
در حالت اول، یعنی در وضعیت استاتیکی، آزمون ضربه با شوک آنی و سقوط آزاد انجام میگیرد. قطعه تحت آزمون در جای خود قرار میگیرد و دستگاه شارژ میشود، سپس با یک عمل مکانیکی وزنه رها میشود، نیروی وارد شده مبتنی بر همان شتاب جاذبه زمین است.
در آزمون ضربه دینامیکی، اثر شتاب حذف میشود. زیر دستگاه از یک جک هیدرولیک استفاده شده است. جک آهسته آهسته به قطعه اجازه میدهد که با تغییرات نیرو هماهنگ شود و با تغییر، فرم بگیرد. در این حالت تغییر شکل شاخص ارزیابی است. بعد از تغییر فرم با ابزارهای دیگر زاویه گردش یا چرخش کنترل میشود.
دستگاه آزمون دیگر، تَرَکیابی به روش ذرات مغناطیسی (Magnetic Particle Test) است. این دستگاه برای قطعات فورج، به ویژه شفت کوتاه و بلند که مستقیماً کوپل به آن وارد میشود، کاربرد دارد. بر روی تمام قطعات فورج این آزمون غیرمخرب به صورت صددرصد انجام میشود.
چه الزامی برای انجام این آزمون به صورت صد در صد برای قطعات فورج داشتهاید آیا الزام مشتری است؟
خیر؛ الزامی از خارج مجموعه یا مشتری به ما تحمیل نشده است. ما شاهد آن بودیم که در فولادهای ورودی و قطعات فورج مشکلات زیادی وجود دارد، فولادهایی که خریداری میشود هرچند تاییدیه فروشنده را دارند، ولی بینقص نیستند؛ بنابراین با صرف هزینه، دستگاه مخصوص ترکیابی را برای آزمون قطعات فورج تهیه کردیم. ما حتی چهارشاخه و کاپهای چهارشاخهها را هم با این دستگاه ترکیابی میکنیم.
از آنجا که جا زدن کاپ یک فرایند نیروبر است که ضربه باید زده شود تا کاپ جا برود، پس احتمال ایجاد ترک همیشه وجود دارد. وجود ترک در چهارشاخه به ویژه در کاپ بسیار خطرناک است. حتی به صورت تصادفی بر روی خارهای فابریک روی چهارشاخه و خارهای بلبرینگ هم آزمون ترکیابی انجام میشود.
تمام این فعالیتها زمانبر و هزینهبر است وهیچ الزامی هم از جانب مشتری نبوده است، ما بنا به اهتمام به تولید با کیفیت بالاتر، خود را موظف به انجام این کارها میدانیم.
اگر مشتری شکایتی از قطعات داشته باشد، چگونه پاسخگو هستید؟
ابتدا گروهی از بخش مهندسی وکنترل کیفیت برای ریشهیابی و یافتن علت نارضایتی به محل فرستاده میشود.
اگر بنا به تشخیص گروه یادشده، نقص فرایند در یک ایستگاه باعث نارضایتی شده باشد، خط تولید در آن نقطه متوقف میشود. بخشهای کنترل و تضمین کیفیت، بازنگری لازم را انجام میدهند. همچنین سوابق، آمار تولید و گزارشها بررسی میشوند تا مشخص شود تولید مرتبط با چه روزی بوده است. برچسب شناسایی ردیابی محصولات ما بهروز است. در این مورد نیز الزامی از جانب مشتری نداشتهایم. معمولاً مشتریان خواستار برچسب تولید ماهانه هستند، ولی در سال جاری برچسبها به صورت روزانه انجام میشود. با اوصاف یاد شده کاملاً مشخص است که ایراد محصول در کدام ایستگاه بوده است.
در ایستگاه آخر و حتی در خط رنگ، بخش کنترل کیفی گزارش کیفی حاصل از آزمون صد در صد قطعات را میگیرند. الزاماتی که در مورد گاردان در دو ایستگاه آخر در نظر گرفتیم، بار مالی زیادی بر دوش شرکت بهسوز خودرو آبی گذاشته، ولی حاصل کار بسیار رضایت بخش بوده است.
در گام بعدی، بر روی مستندات گزارشها کار میکنیم. در بخش مهندسی نقشهها بازنگری میشود و پس از آن کمیسیونی تشکیل می-شود که در آن دیدگاههای مختلف و موارد گوناگون بررسی میشود تا علت دقیق مشکل روشن شود.
در سوابقی که تاکنون داشتهاید، چند درصد برگشتیها مربوط به آزمون و آزمایشگاه میشود؟ یعنی نداشتن کدام تجهیزات آزمون مناسب باعث بروز ایراد شده است؟
درصد بسیار بالایی از آمار برگشتی قطعات، مربوط به آزمون است. تولید گاردان فرایند چندان دشواری نیست، ولی انجام فرایندهای آزمون گاردان بسیار مهم و پیچیده است. به جرات میتوان گفت که در تولید گاردان، ایستگاههای آزمون اهمیت بیشتری از خود فرایند تولید دارند.
برای حل مشکلات احتمالی، پیش از ایستگاه مونتاژ، کنترل صددرصد انجام میشود. تمام قطعات ماشینکاری قبل از ورود به مونتاژ، از نظر انحراف از محور، اختلاف ارتفاع، انحراف محور و run out کنترل صددرصد میشوند. این سه ویژگی در قطعاتی که به هم متصل میشوند، اهمیت زیادی دارد. فیکسچر، گیج و ابزار کنترلی مستقل برای کنترل پارامترهای یاد شده طراحی کردهایم. در این بخش قطعات به صورت کشویی غلافی متصل میشوند. پس از اتصال نیز قطعه run out گیری میشود تا پس از مونتاژ، خطایی نداشته باشد. انحرافهای کوچکی که در هر قطعه ایجاد میشود، در ایستگاه آخر برای آزمون نابالانسی گاردان عددی بزرگ وغیرقابل چشمپوشی خواهد شد. به همین دلیل مصمم هستیم که در آینده گاردان نهایی را هم دوباره run out گیری کنیم.
آیا برای چنین کاری هم الزام مشتری را داشتید؟
تنها روی سه نقطه لوله برای ما الزام وجود دارد. روی سه نقطه با فاصلههای مشخص از تکیهگاه روی لوله ملزم به انجام آزمون هستیم. میخواهم بر این نکته تاکید کنم که حتی اگر الزامی از جانب سفارشدهنده نباشد، ما برای بهبود کار ناچاریم این آزمونها را به صورت صددرصد انجام دهیم؛ زیرا در غیر این صورت دوبارهکاری زیاد میشود. فرایند آزمون صددرصد با آنکه بسیار پرهزینه است، برای ما بسیار حیاتی است. ممکن است حتی ناچار شویم دو خط جوشکاری داشته باشیم. شرکتهای تولیدکننده گاردان به ندرت run out را در انتهای خط انجام میدهند. اما ما خودمان را ملزم به این کار کردیم. مشتری هم به صورت تصادفی و نه صددرصد آزمون را انجام میدهد.
در خط تولید بهسوز خودرو آبی دو آزمون صددرصد وجود دارد؛ نابالانسی و run out گیری. علاوه بر اینها، در ایستگاه بستهبندی تمام اتصالات دوباره چک میشوند. خارهای مفصلهای چهارشاخه، تک تک بررسی میشوند چون در فرایند تولید جا زدنشان دشوار است. این مهمترین مزیت رقابتی برای شرکت بهسوز خودرو آبی به شمار میرود.
بدیهی است که این نگرش، یعنی تمرکز بر آزمون در تولید اختلال ایجاد میکند و آمارتولید را کاهش میدهد. دیدگاه مدیریت ارشد شرکت در این زمینه چیست؟
این شیوه دقیقاً، خواسته مدیریت ارشد مجموعه است. آقای مهندس نوری هیچگاه در زمینه هزینه کردن برای افزایش کیفیت محدودیتی در نظر نگرفتهاند. برای حل مشکل کاهش تولید، زمان تولید را افزایش دادیم و شیفت کاری را به دو یا سه شیفت رساندیم.
گاهی در زمانهای خاص آمار تولید قطعات نیمهساخته را بالا میبریم و مطلقاً اجازه نمیدهیم وقفهای به وجود بیاید.
درصد MRP شما برای گاردان نیسان و گروه بهمن چقدر است؟
برای نیسان نود درصد نیاز خط را ما تامین میکنیم. تامین 2250 قطعه به عهده ماست. حداکثر تعداد نیز حدود 3200 قطعه بوده است. در گروه بهمن در یک مورد ما تنها تامینکننده هستیم و تولید گاردانهای DAE و OHVG بر عهده ماست. البته در مورد مزدا تامینکننده دیگری هم وجود دارد.
در زنجیره تامین ایران خودرو قرار ندارید. چرا؟
در حال حاضر با ساپکو همکاری نداریم. تمایل داریم به نقطهای برسیم که در تولید منظم مزدا و گروه بهمن و گروه سایپا به نقطه ثبات برسیم، پس از آن بر مبنای حجم مازاد توان و برآورد پتانسیل باقیمانده، قصد همکاری با سایر گروهها همانند ساپکو و تراکتورسازی را داریم.
ما مایل هستیم مشتریان متعدد داشته باشیم؛ زیرا وابستگی به یک مشتری و نوسانات پرداختیها و دریافتیها برای تولید، سکته ایجاد می-کند و دردسرساز است. قصد داریم سبد کالایمان را افزایش دهیم تا در شرایط مختلف و سختی که ایجاد میشود حمایت مالی لازم را داشته باشیم و دچار فشار مالی نشویم. الان روی دو گروه داریم کار می کنیم.
آیا از نظر دانش فنی در تولید گاردانهای خانواده پژو، ضعفی ندارید؟
خیر؛ هیچ نمونه داخلی برتر از تولید شرکت بهسوز خودرو سراغ ندارم. تلاش ما همواره بر این بوده که تمام عیبهای فرضی را برطرف کنیم و هر روز محصولی برتر از روز قبل به دست مشتری برسانیم.
بسیار سپاسگزاریم از این که وقت خود را در اختیار ما گذاشتید.
مهمترین مزیت رقابتی شرکت بهسوز خودرو آبی انجام دو آزمون نابالانسی و run outگیری قطعات در خطوط تولید است که این کار با هزینهای نسبتا بالا به انجام میرسد اما باعث افزایش کیفیت محصولات و جلب رضایت مشتریان شده است.